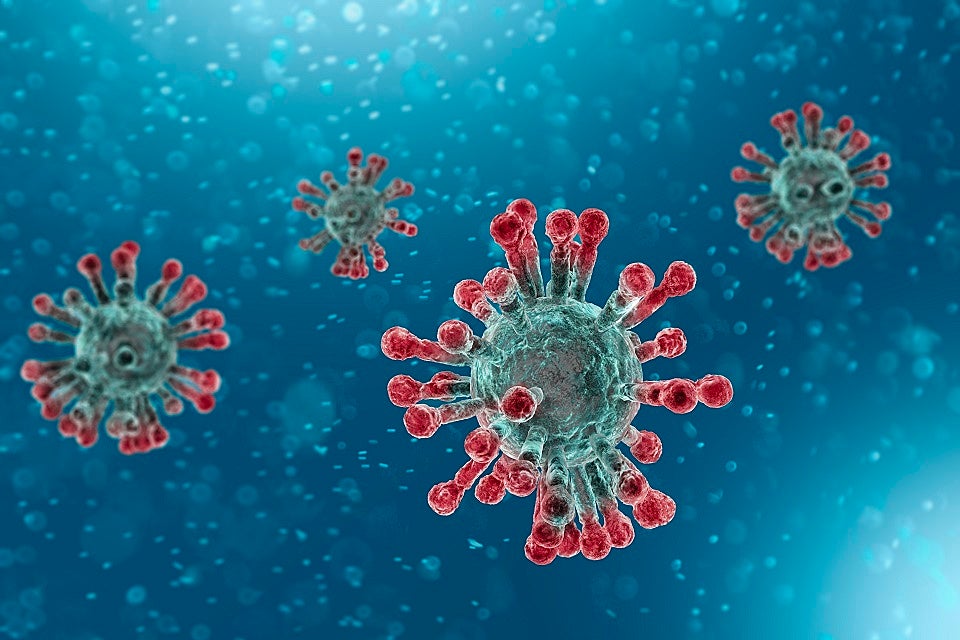
by Stuart Davey BSc MRQA.
In early 2020, Butterworth Laboratories Ltd (Butterworth) were eagerly anticipating a letter from the MHRA informing us of the intent to carry out a regulatory inspection of our premises, as our last inspection had been in August 2017. January, February and March came and went with no notification.
Then came the somewhat sudden escalation of the Covid-19 crisis and the commencement of the UK lockdown. As Government advice surrounding the Coronavirus lockdown restrictions were announced, we instigated our Covid Business Continuity Plan, and on the 23 March 2020, we had taken the decision to move all members of staff that we are able to do so to home working. This included the entire QA team. Then, on the 6th April 2020, a formal notification was received from the MHRA stating their intent to perform a remote audit of BLL for GLP compliance on the 28 and 29 April 2020.
Remote regulatory inspections: the MHRA
Butterworth had never hosted remote regulatory inspections before and hence we were not sure what to expect – would this mean sitting in front of a laptop all day and setting up a ‘virtual’ office whilst watching the inspector at work and answering ad hoc questions? Would it mean searching for ad hoc information requests for two whole days? How would we bring in experts for answering technical questions? Whatever the format we all agreed that this would be a challenge but we were ready for it.
Some of our questions would be answered on the 16 April 2020 when an email was received from the inspector requesting documents and information be sent in advance of the inspection. The requests were numerous and took several days to put together but one thing in our favour was that we had an electronic QMS and the fact that we scan nearly every GxP related record and document to our electronic documentation system. This meant that even working from home, we could readily retrieve electronic copies of everything requested and send them via email to the inspector.
The opening meeting was scheduled for 11 am on the 28 April and was to be conducted via Zoom. At the opening meeting, the inspector stated that he had never conducted remote regulatory inspections before so this was a new experience for all concerned (which provided us with a modicum of relief).
At the opening meeting, the inspector stated that, due to the circumstances, this would be a general inspection of the GLP systems in place and would not be concentrating on the review of study-specific raw data, which would be performed at a later date when an inspector was able to physically visit the site. The inspector requested some additional information based on a review of information already sent, and the opening meeting came to a close.
During the course of the inspection, as more information was requested and questions asked, we used the screen share function in Zoom to more easily and readily look at the same documents at the same time. This worked really well and avoided having to play email tennis. In fact, it worked so well that there was no discernible difference than if we were having a face-to-face inspection and questions were easily answered, understood and dealt with. As a result, the inspector was able to get through a lot in a short space of time.
During the closeout meeting, the inspector praised our systems and in particular our ability to retrieve information in rapid time despite the circumstances.
Our first remote client audit
A few days after the GLP inspection BLL was contacted by a potential new client who also wished to perform a remote audit of us. Now we were confident in our abilities to host remote audits we scheduled this client audit in immediately. As the client had no previous knowledge of our systems, the client audit was, if anything, more demanding in terms of requests for information than the MHRA inspection. However, it too went very smoothly and once again we were praised for the speed with which we were able to deliver documentation and information requests.
On this basis, we were approved as a supplier by the client.
Final thoughts
Both experiences were very positive and it became clear to me that the use of technology for conducting remote inspections has been a much-underused tool in the Pharmaceutical industry. The current method of physically auditing a site every two or three years now appears to be quite wasteful in terms of money and time spent, in addition to the impact on the environment from travelling to and from sites.
It occurs to me that, having been forced to think about new ways of conducting business, the industry has an opportunity to rethink traditional ways of working which will bring benefits not only to individual companies in the industry but to the environmental health of the planet. Perhaps companies might alternate on-site audits with remote audits every two years? There are lessons to be learned certainly and it remains to be seen whether the industry is ready to change.