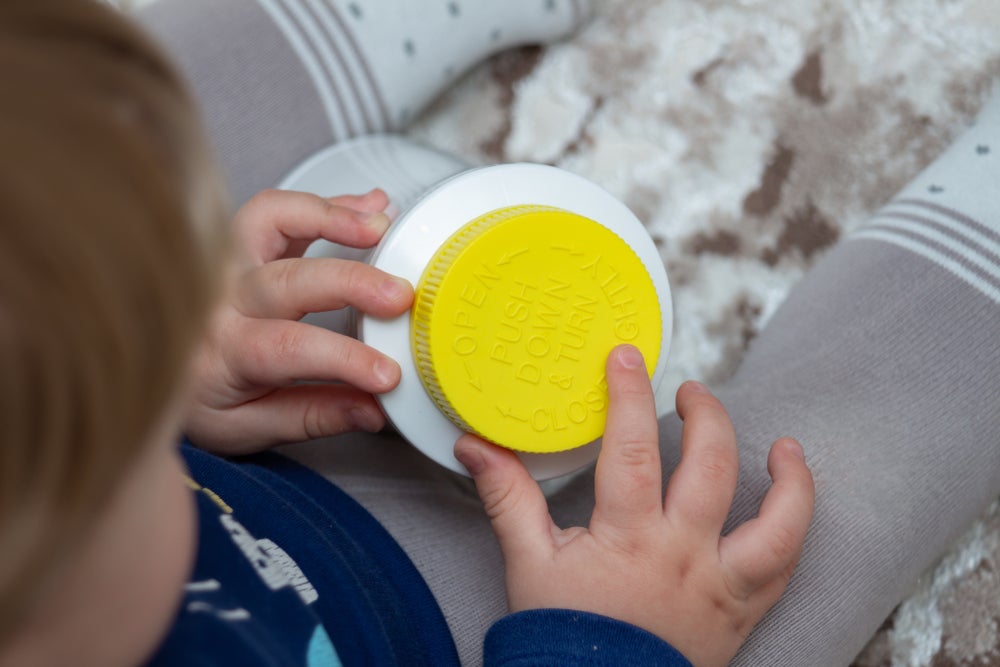
While childproof packaging for pharmaceuticals is of fundamental importance and an ethical duty for the industry, multiple drugs in recent years have failed to meet regulatory requirements leading to recalls.
In March, Pfizer was forced to recall its Nurtec ODT migraine drug, which it obtained through the acquisition of Biohaven, because it did not meet the standards for child-resistant packaging (CRP) requirements. Other recent recalls have also been made for similar reasons in the last few years, including Nationwide Pharmaceutical’s ferrous sulfate iron tablets in 2023, Novartis’s cancer drug Zofran and heart drug Entresto in 2018, and Sandoz’s anti-psychotic, haloperidol, the same year.
The growth in child-resistant packaging market is thought to be fuelled in part by the increased presence of medication in our homes as more adults are prescribed sleeping aids, opioid painkillers, and antidepressants. A rise in the use of medicinal cannabis and CBD products is also important to consider from a child-safety perspective. As per Public Health England, 70% of poisoning admissions of children under the age of five are caused by medicines.
Pfizer and Nurdec ODT
Earlier this year, Pfizer recalled more than four million packages of the Nurtec ODT prescription migraine medication due to the product being sold in packaging that is not child resistant. The recalled drugs were required to be in child-resistant packaging as per the Poison Prevention Packaging Act.
“The issue appears to have arisen during the acquisition of Nurtec ODT in October 2022,” says Jon Lant, head of new product development and innovation at Origin, a UK-based company providing pharmaceutical packaging solutions. “[This means] Pfizer essentially inherited the problem. After learning the medication’s packaging didn’t meet the requirements for child safety during the company evaluation, Pfizer alerted the US Consumer Product Safety Commission. But there really is no excuse to bring a medicine to market that fails to have the right (and compliant) child safety features.”
How well do you really know your competitors?
Access the most comprehensive Company Profiles on the market, powered by GlobalData. Save hours of research. Gain competitive edge.

Thank you!
Your download email will arrive shortly
Not ready to buy yet? Download a free sample
We are confident about the unique quality of our Company Profiles. However, we want you to make the most beneficial decision for your business, so we offer a free sample that you can download by submitting the below form
By GlobalDataSee Also:
Lant says that while Pfizer worked on creating new child-resistant packaging for the product, consumers were recommended to keep the medicine out of reach of children and to request a child-resistant pouch to store the medicine in the meantime. Pharmacists were also required to place the blister packs into vials with child-resistant lids when filling patient prescriptions.
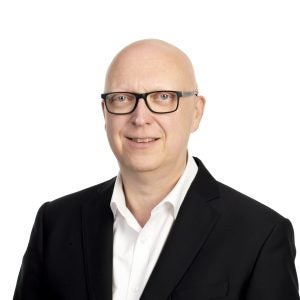
While there were no reports of child poisoning in relation to this incident, it highlights the importance of child-resistant packaging and the need for due diligence within big pharma during the merger and acquisition process.
Regulatory requirements
There are four global regulatory standards in the packaging space, with compliance depending on where the product and packaging will be sold: BS EN ISO 8317:2004 – an international standard aimed at reclosable packaging; BS EN 14375:2003 – a European standard aimed at non-reclosable packaging for medication packaging; BS EN 862:2005 – a European standard aimed at non-reclosable packaging for non-medication packaging; and 16 CFR 1700.20 – an American regulation, which covers both reclosable and non-reclosable packaging.
To be awarded these certifications, the packaging in question must be trialled by a group of 200 children between the ages of 42 to 52 months.
Lant explains, “Two tests take place with five minutes given to the children to attempt to open the packaging; before an adult demonstration and then after an adult demonstration. If at least 85% of these children fail to open the packaging within five minutes (before the demonstration) it passes. However, this drops to 80% after the demonstration.”
He adds that a hallmark of child-resistant packaging requires the ability to simultaneously complete two distinct motions such as ‘push and twist’ or targeted pressure on a blister pack. However, the latest designs in pharma packaging also include: perforated blister packs requiring a bend and tear movement; lids that require moisture (water) before the peel may be removed and the bottle opened; PET laminates with laser perforation, requiring tension, a specific point, in a linear motion to open the packaging; and flexible pouch packaging with a flap disguising the opening with a ziplock feature. Additionally, visual distraction technology, which distorts depth perception on packaging, makes it difficult for children to understand and perceive how to open it.
Overcoming the challenges in child-resistant packaging
There are several considerations that manufacturers and packaging technologists can consider when designing child-resistant packaging for medication. Pharmaceutical packaging needs to protect children whilst also offering ease of access to older and less able people who may struggle with sight or dexterity. Packaging innovation plays an important role in overcoming this challenge.
“For instance, lids that require moistening before opening are very easy for any adults to open but will prove challenging for children under five,” says Lant. “For packaging to be considered senior-friendly, it must also pass a test. Ninety percent of the testing group must be able to open and close the package within five minutes. It must comply with the following UK regulations: BS EN 8317:2015 and BS 8404: 2001.”
Another is to balance child safety while investing in sustainability. As with all industries, sustainability and environmental impact have become key considerations in recent years. However, the responsibility of protecting children from accidental ingestion and poisoning must be the priority.
“Traditional plastic has long been relied upon and proven effective in creating child-resistant packaging for pharmaceuticals,” Lant comments. “This long-lasting reliance makes changing what works a challenge, but something the industry is working to overcome.”
“The mass adoption of Quality by Design is vital for addressing this pervasive issue,” says Lant, “ensuring all packaging and delivery components are precision designed and engineered so they’re delivered and administered to patients as intended. Child-resistance, as well as accessibility for less able or senior people, should be included here too as nations around the world experience the impacts of ageing populations and more complex health needs.”